Live
- Boxing Day Test Weather Forecast: Rain Delays Expected on Day 3 and Day 4 in Melbourne
- Baby John Twitter Reviews: Varun Dhawan Impresses, But Fans Feel the Remake Lacks Theri's Charm
- Pakistan Air Strikes Kill 46 in Afghanistan, Taliban Confirms Amid Rising Tensions
- ACB Launches Investigation into Formula E Races Held in Hyderabad Last Year
- Mega Job Mela in Madhapur on December 28: Explore Employment Opportunities in Hyderabad
- New Mizoram Guv likely to take charge next week
- Barroz 3D Movie Review: A Visual Treat for Mohanlal Fans, Mixed for Others
- Donate Blood, Save Lives: BJP Hosts Mega Blood Donation Camp in Aiza
- Azerbaijani Airliner Crashes Near Aktau, Kazakhstan: 32 Survive, Over 30 Feared Dead
- Union Minister Bandi Sanjay Kumar to Visit Jogulamba Gadwal District on December 27, 2024
Just In
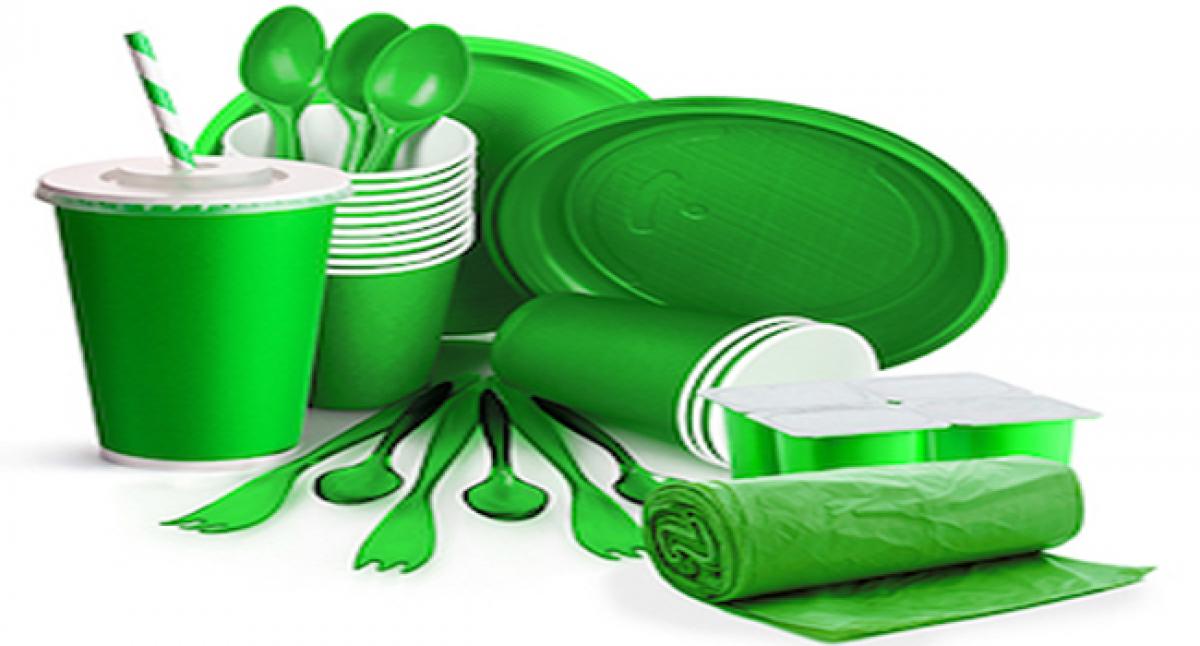
In the early 1940s, Henry Ford experimented with making plastic parts for automobiles He came up with what was called the plastic car made from soybeans
Kolkata (IANS/Mongabay): In the early 1940s, Henry Ford experimented with making plastic parts for automobiles. He came up with what was called the "plastic car made from soybeans."
Since that decade, when mass plastic production began from oil-based materials, its use has surged dramatically, becoming a big part of our daily lives. The resulting unwanted plastic pollution crisis and awareness of depleting fossil fuel reserves has driven research toward alternative, sustainable materials.
Extending the hunt for sustainable materials as an alternative to fossil fuel-derived plastics, Indian scientists at the International Crops Research Institute for the Semi-Arid Tropics (ICRISAT) are working with the humble drylands crop plant sorghum (jowar) and a bunch of microbial minions to help shape a bio-based plastic future.
Commonly used bioplastic feedstocks (raw materials) are: cellulose, starch, glucose and vegetable oil. "We need a good amount of feedstock. Sorghum is a rich source of starch like corn and potato. Starch based edible cutlery is popular across the world," A Ashok Kumar, sorghum breeder at ICRISAT, told Mongabay India.
"Currently people are using sugarcane bagasse as source material for bioplastic but here we have developed a sorghum that is far more effective for biomass-based plastic and will be much cheaper and more sustainable," Ashok Kumar said. He was referring to sorghum cultivars (RVICSH 28 and ICSV 18542) that have high biomass yields and more ratoonability (yielding more than one harvest from a single planting) making them amenable for crafting into bioplastics.
"In line with sugarcane, corn, cassava and sugar beet, high biomass sorghum has very good potential with wider adaptability, is fast growing (completes life cycle in four months), and has high biomass production with its efficient C4 photosynthetic pathway. It can be grown in rain fed conditions with low-nutrients," Ashok Kumar said.
Sorghum biomass specifically is transformed into polylactic acid which is further processed into bioplastic. In the transformation process, sorghum bagasse has to go through sacharification, fermentation and polymerisation. Bacterial fermentation of sugars derived from sorghum biomass produce lactic acid which is then synthesised by polymerisation to produce polylactic acid.
Ashok Kumar explained when starch is used as feedstock it is put through a sacharification process using enzymes to produce liquid glucose. Special bacteria or fungi can produce lactic acid monomers from liquid glucose. The monomer is then polymerised to produce polylactic acid, a biodegradable polymer.
"Whatever chemicals are used for generating normal plastic from oil, the same are used here. The major difference is that you are tapping into plant-based raw material. So it is biodegradable but you make it synthetically," Kumar said.
A single search online is indicative of the slowly changing narrative, in favour of bioplastics. Carry bags for shopping, packing material for food items and meats, bin liners for hotels, cutlery, nursery plant pots and trays, wet waste compost bag, plant seed bag, cling wrap, food wrapper and a plethora of products made from plant-based materials vie for attention.
Do-it-yourself (DIY) "plastic from starch" videos are also part of the throng on sustainable solutions. The production and use of bioplastics is considered as a sustainable solution due to low emission of greenhouse gasses.
But there are challenges too at both ends of the production cycle. It takes a significant amount of energy to manufacture these plastics and there are question marks on their biodegradability.
Can bioplastic fit in within the current industry infrastructure and does it put pressure on forests (to convert into land for growing feedstock plants)? For starters, the ICRISAT Microbiology Team has in hand three microbial strains that can speed up the breakdown of the used bioplastic mass (64 per cent degradation in 60 days).
"We identified certain microbes (Myceliophthora thermophila ATCC-48104, Aspergillus awamori and Bacillus subtilis) that will degrade the bioplastic very quickly. They are also biodegradable by themselves but you can hasten up the degradation with any of the microbes," he said.
Although, at this stage bioplastics are slightly costlier than normal petrochemical-derived plastics and can't be moulded into a variety of things, Ashok Kumar asserts it is worth the effort and expense. Currently, bioplastics represent about one percent of the about 320 million tons of plastic produced annually.
A report by UN Environment that assesses the potential of replacing certain conventional plastics applications with alternative materials states that is neither possible nor desirable to remove all plastics from society, but alternatives can have a significant role in reducing our dependence. (In arrangement with Mongabay.com, a source for environmental news reporting and analysis)

© 2024 Hyderabad Media House Limited/The Hans India. All rights reserved. Powered by hocalwire.com