Live
- Advocates Protest Misleading Land Allocation for Jogulamba Gadwal District Court Complex
- Good Swimmer, Lifejacket On’: Brother of Missing Man Holds Hope After Mumbai Boat Accident
- TTD Invites Proposals for 'Tirumala Vision-2047' Development Plan
- Champions Trophy 2025 Venue Revealed: India, BCCI Face Setback After ICC 'Compromise' Decision
- Apple vs. Meta: Privacy vs. Interoperability Under the EU’s Digital Markets Act
- District Collector Urges Swift Completion of Pending Construction Projects
- KTR Faces Case Over Rs 45-Crore Payment for Formula E Race in Hyderabad
- HYDRAA Demolishes Illegal Shops in Manikonda’s Alkapur Colony Amid Protests
- Why Dates Are a Winter Superfood: Top Health Benefits of Khajoor
- District Judge Ganta Kavitha Devi Conducts Surprise Inspection at Gadwal Government School
Just In
Driving Innovation in Semiconductor Manufacturing: A Veteran's Role in New Product Management and Global Supply Chain Coordination
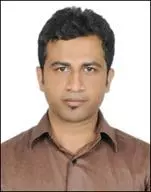
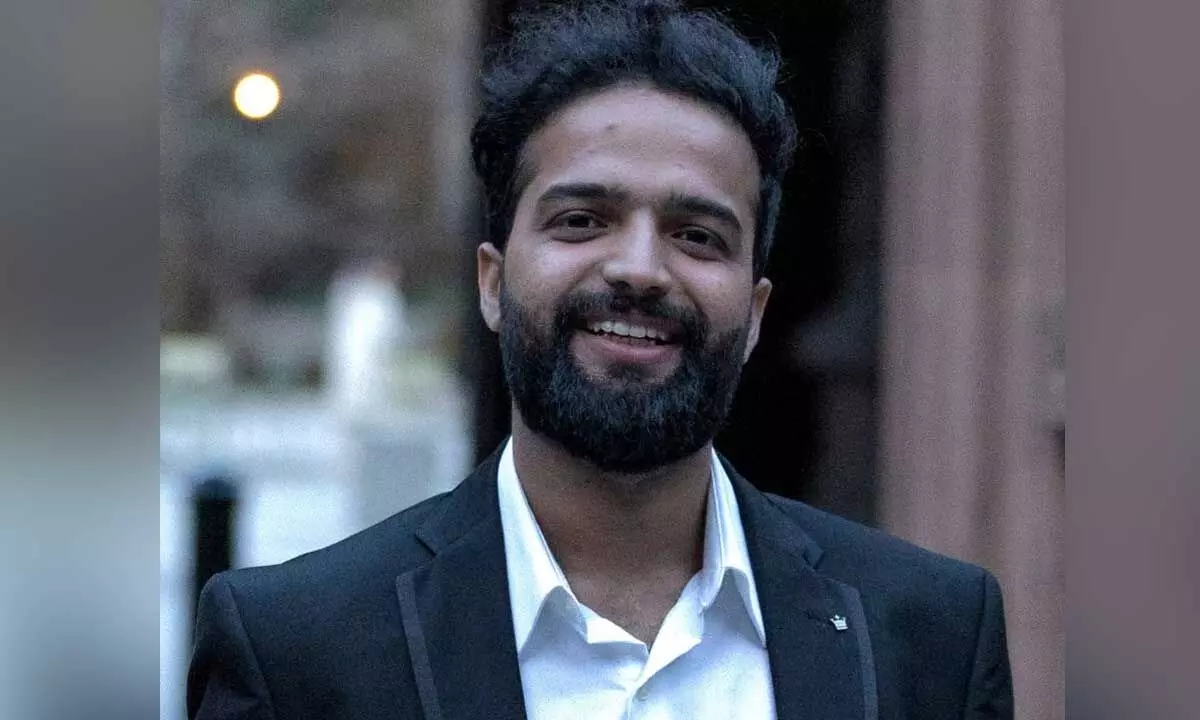
The landscape of the semiconductor industry is dynamic and progress-driven; therefore efficiency or innovation will not be a matter of choice but a requirement to thrive in such a field characterized by rapid technological changes and ever increasing performance requirements.
Bengaluru: The landscape of the semiconductor industry is dynamic and progress-driven; therefore efficiency or innovation will not be a matter of choice but a requirement to thrive in such a field characterized by rapid technological changes and ever increasing performance requirements. There is almost always a race to create smaller, faster, and more power efficient chips, and at the same time enhance the processes to be cheaper. With the increasing need for semiconductors worldwide, these businesses need to be flexible and learn new ways and materials to be able to provide the best solution.
A series of by Shubham Ekatpure, within this field exemplify how strategic thinking, advanced technologies, and cross-functional collaboration can drive substantial improvements in both production processes and cost management.
Leading the deployment of five advanced semiconductor packaging machines, he comments, “This initiative, which involved orchestrating the full supply network deployment across over 200 suppliers, showcased the intricate coordination required to manage a global supply chain”. Collaborating with teams of more than 100 engineers, the project ensured that these cutting-edge machines entered the market on schedule. By managing risks, optimizing capacity, and negotiating costs, the deployment accelerated time-to-market and bolstered the organization’s ability to compete in the semiconductor industry.
In the domain of cost management, innovation took center stage with the development of a Python-based "should cost" model for semiconductor equipment. This groundbreaking tool, a first-of-its-kind, estimates the cost of tools valued at $1–2 million with an impressive accuracy rate of 5%. The model integrates data from multiple sources, including prototyping costs and component prices, and has become an integral part of Cost of Goods Sold (CoGS) calculations. As a result, it now informs production quotes, financial assessments, and materials budgets, providing vital insights for strategic decision-making.
Supply chain resilience also came into focus during the COVID-19 pandemic, when disruptions to electronic components for Printed Circuit Board Assemblies (PCBAs) and Power Supply Units (PSUs) posed significant challenges. To address these disruptions, he developed a Python-based risk management tool. This tool, which leverages APIs such as Octopart, Cofactr, and Z2 Data, monitors global inventory patterns for over 3,000 components and assesses supplier vulnerabilities. By collaborating with external partners, the tool was enhanced to automatically purchase high-risk components, thereby mitigating supply disruptions and positively affecting profitability.
Further advancements in capacity planning were realized through the development of a simulator designed to analyze the entire supply chain for a business unit producing six diverse products. Each product came with Bills of Materials (BOMs) containing tens of thousands of lines. Using Python and integrated with the Oracle ERP API, this simulator consolidates BOMs, manages demands within the supplier base, and optimally allocates resources.
Strategic process improvements yielded significant cost savings. “Through expert procurement and negotiation strategies, expenditures for over 1,000 unique parts in low-volume, high-mix assemblies were managed, resulting in $10 million in cost savings over the product lifecycle”. Informs Shubham. This achievement not only enhanced financial performance but also demonstrated how a strong focus on cost optimization can benefit both the company and its stakeholders.
The creation of a web application used by more than 500 employees across engineering and supply chain departments in the U.S. and Singapore was remarkable. Built using Python, his application tracks orders, inventory, and supply chain KPIs for new product sourcing. By improving transparency and streamlining decision-making processes, it enabled teams to better manage supply chain operations and new product sourcing.
Reportedly, a full-cycle Six Sigma project also achieved a remarkable 12% reduction in inbound freight costs, equating to annual savings of approximately $80,000. By analyzing data in Minitab, strategies were developed to streamline logistics and reduce expedited freight expenses, further optimizing supply chain costs and improving operational efficiency.
Moreover, the outsourcing of over 10 complex assemblies during the New Product Introduction (NPI) phase proved to be a major milestone. By offloading complex vision and mechanical assemblies to external suppliers, in-house production burdens were reduced, allowing the organization to focus on its core competencies and cut costs.
In conclusion, these projects highlight the intersection of innovation, strategic planning, and technical expertise in semiconductor manufacturing. By leading these initiatives, Shubham Ekatpure and the team was able to drive substantial improvements in cost management, supply chain resilience, and production efficiency. The positive impact on the organization’s financial performance and market competitiveness underscores the importance of continually pushing the boundaries of what is possible in this fast-paced, high-tech industry.

© 2024 Hyderabad Media House Limited/The Hans India. All rights reserved. Powered by hocalwire.com